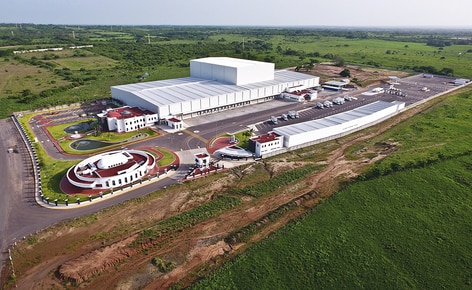
DECASA, the most important consumer products distributor in Mexico, builds a distribution centre with systems that improve picking quality and productivity
Multiple storage solutions streamline the distribution of consumer products at DECASA
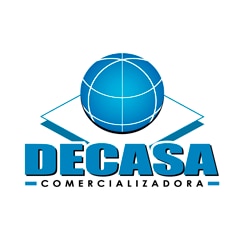
The DECASA logistics centre in the state of Veracruz features a wide variety of solutions: an automated clad-rack warehouse, the semi-automatic Pallet Shuttle, multi-level picking towers for pallets and boxes, a sorter, etc. The installation, with a capacity for more than 36,500 pallets, is also run by the Easy WMS Mecalux and the Galileo control programme.
About DECASA
The growth experienced in recent years has made DECASA the largest distributor of consumer products in Mexico, covering more than 80% of the domestic territory.
Founded in 1980, DECASA has a highly-talented workforce, state-of-the-art technology and the most grandiose storage and distribution infrastructure in the sector. Currently, the company offers 7,000 consumer products divided into several categories: food, cleaning and home care, paper, personal hygiene, pet foods, wines and sweets.
With over 350 suppliers, 2,700 employees and sales increasing every day, DECASA owns and runs six distribution centres in leading business-driven cities (Veracruz, Puebla, Guadalajara, Torreón, Aguascalientes and Cortazar) from where it distributes more than 5,000,000 boxes of products a month. Moreover, 90% of these distributed products are delivered within 24 hours.
DECASA has expanded into other types of businesses, such as self-service locations for the general public and cash & carry centres, for retailers.
The needs of DECASA
The company needed to build a new warehouse to pick and locate its wide variety of products, from small-sized items to bulky products.
To do so, Mecalux has designed and installed multiple storage solutions that yield results in company operations. The 22,000 m2 logistics centre was installed in the Industrial Park of Santa Rita, a more than 200 hectare industrial and commercial complex located in the state of Veracruz (Mexico).
In addition, the installation has been built taking into account the future growth of the company.
Mecalux's solution: eight warehouses in one
From the beginning, Mecalux worked closely with those responsible for the different phases of civil engineering and those in the logistics management at DECASA to determine which solution was the best fit for the company's needs. The result is a warehouse where different systems are combined, resulting in eight different zones:
1 & 2. Self-stacking zone and future expansion: pallets with large products are stored one on top of the other on the warehouse floor. DECASA also has a 2,000 m2 area that will permit storage capacity to be enlarged in the future.
3. Automated clad-rack warehouse: this consists of eight double-deep aisles that can store more than 28,000 pallets in a total area of 4,610 m2, primarily set aside for products DECASA purchases from its suppliers.
4. Pallet Shuttle warehouse: two levels of high-density racks with the semi-automatic Pallet Shuttle system were installed on a mezzanine floor located in front of the docks. They have a capacity for 512 pallets of lightweight and bulky products.
5. High-rise picking: three blocks with five floors per block were set up, each with an intermediate walkway; three for picking and two for reserves. To prepare orders, operators deposit SKUs on a conveyor circuit that crosses through the central part of the different picking floors.
6. Pallet racking: here lower demand products are picked, and reserve goods are stored to be used in picking later on.
7. Order classification: the installation features a full conveyor circuit connecting the high-rise picking towers with a huge sorter that flows to the loading docks.
8. Loading docks: the DECASA warehouse has 21 loading docks (10 entry and 11 exit) just in front of the sorter and Pallet Shuttle warehouse.
The various solutions
Automated clad-rack warehouse
Mecalux erected an automated clad-rack warehouse on a 4,610 m2 surface, which is approximately 30 m tall with a capacity for more than 28,000 pallets of 1,000 x 1,200 mm with a maximum weight of 1,300 kg. Here DECASA deposits the products its purchases from its suppliers.
The warehouse consists of eight 68 m long storage aisles with double-depth racks on both sides and 14 load levels. The double-depth racks are best known for providing high storage capacity.
Two stacker cranes were supplied, to finish off the operation, which are responsible for handling the goods from the positions at the front of the warehouse to the corresponding rack location, as well as a transfer car that links the storage aisles and the input and output stations of the warehouse.
Stacker cranes increase productivity, decrease the resources required to handle the goods and reduce errors through automation. These machines are guided by the Galileo control programme. For its management and integration with other storage systems, DECASA has incorporated the Easy WMS warehouse management software by Mecalux.
When working with perimetral type pallets (with open skids on all four sides), perpendicular cross ties were placed on the rack beams to support the pallets and thus ensure the stacker cranes handles them safely. This type of pallet improves stability during refitting.
Before entering the automated warehouse, the merchandise goes through a checkpoint that validates if it meets the requirements for its location in the warehouse.
Transfer bridge
In a warehouse with a huge number of movements, it is almost always essential to have a stacker crane in each aisle. However, in DECASA's case, it has prioritised cost savings over the turnover of the goods, which is why just two stacker cranes are arranged to manage eight aisles.
The stacker cranes change aisles automatically, thanks to a transfer crane placed at the end of the aisle. This machine, to which the stacker crane is anchored, moves conjointly from one workspace to another.
The whole system is set up to maintain the required safety levels of each installation and prevent the stacker crane from slipping out of the lower guide rail when the transfer bridge is not centred in its aisle.
Features of a clad-rack warehouse
The company opted for a clad-rack warehouse since this construction occupies only the strictly required space and volume. They are formed by the racks themselves, onto whose structure the roof and side walls are coupled. When designing the building, one must anticipate numerous factors, including the loads of stored goods, the forces exerted by the handling equipment, the force transmitted by the wind, the corresponding seismic coefficient of the area where it is installed or the local regulations in force.
Tubes in the fire safety system are installed and fixed to the racking, thus shielded from occasional impacts and enabled to spray pallets properly in case a fire breaks out.
Semi-automated warehouse with Pallet Shuttle
There are two levels of high-density racks with the semi-automatic Pallet Shuttle system installed on a 5 m high mezzanine floor located in front of the docks.
The structure of the rack is adapted so that the electric shuttles can move autonomously inside the storage channel, ensuring a constant flow of merchandise. Thus, forklifts do not have to enter the storage lanes.
This system is ideal to make full use of the available space and to increase the flow of inputs and outputs, while the mezzanine multiplies the useful work surface.
Self-stacking pallet storage
Between the automated warehouse and the multi-level picking installations, there is an area for self-stacking pallet storage on the floor. Over-sized products are deposited in this area.
Due to the durability of the goods and their packaging, pallets can be stored one on top of the other to better max out the available surface area.
Pallet racking
The DECASA warehouse has four blocks of double pallet racking interspersed between the picking towers. All in all, the capacity adds up to 2,890 pallets of lower demand (type C) and bulky products. The top of warehouse stores reserve goods used in the live racking for boxes.
Furthermore, with the help of high reaching order pickers, operators begin to prepare orders by picking directly from the pallet. Once they have finished picking, workers move the SKUs to the front of the loading docks, which await orders to be completed with products from the high-rise picking blocks.
High-rise picking towers
Given that streamlined picking at DECASA is pivotal, three 10 m high multi-level installations were set up where high and medium turnover products (types A and B) are picked. This area, along with the automated clad-rack warehouse, is the heart of the DECASA warehouse.
Each high-rise bay has five floors, three intended for picking and two for reserve products:
- First floor: here picking is done of the smallest items stored in cardboard boxes. To do this, five levels of live racks with rollers are enabled to ensure optimum input and output of material. The goods are introduced into one end and slide via gravity to the opposite side that faces the picking aisle. A conveyor circuit runs centrally along the floor, with racks along both sides.
- Second and third floor: it is similar to the first level, except pallets are housed in the live racking instead of boxes. This high-density storage system fulfils the requirements of the FIFO method: the first pallet in is the first out. Thus, it ensures perfect product turnover, avoids interference in the replenishment and collection of material, and increases picking speeds. Operators, who carry out picking directly from the pallet and work in assigned sectors, deposit the SKUs on the central conveyor circuit. When the pallet is empty, it is introduced into an inverse empty pallet conveyor positioned just below each channel roller.
- Fourth and fifth floor: these floors store reserve product used to prepare orders on the first three levels. On each level, there are two bays of push-back racks that can accommodate four pallets in depth.
Moreover, anticipating the future needs of the company, there is space furbished to install a fourth high-rise bay when necessary.
Spiral lifts
In each multiplex picking area, a spiral conveyor links the conveyors on the first three floors. This 5 m high lift is located opposite the side facing the sorter and pre-loading area.
The conveyors on the first and second floors move the boxes to the lift, while the third-floor conveyor connects to the circuit which flows into the sorter.
Order classification
This area consists of four conveyor circuits –one for each high-rise picking installation–, a recirculation conveyor that redirects the boxes rejected due to some kind of identification error, and a sorter that distributes orders by route and according to a loading sequence.
All orders from the third floor of the high-rise picking installation enter the sorter through an injection circuit. The sorter includes eleven ramps with a combination of roller and belt conveyors.
Management & control: Easy WMS and Galileo
The Easy Mecalux WMS is a powerful, robust, versatile and flexible software that controls, coordinates and manages all movements, and operational processes that go on in this warehouse.
Its aim is to optimise the physical and document management of the flow of goods, from their entry into the warehouse to their final output, ensuring traceability.
On the other hand, the Galileo control programme is responsible for directing all the actions that must be performed by the different moving devices and, thereby, transport the goods between different parts of the warehouse.
Advantages for DECASA
- Optimum capacity: the DECASA logistics centre can store 36,650 pallets in a 22,000 m2 area.
- Planning ahead: the warehouse has a 2,000 m2 section reserved for when the company needs to expand in the future.
- Increased productivity: the various installed solutions multiply the flow of incoming and outgoing pallets, as well as order picking.
- Skilful management: thanks to the Mecalux Easy WMS and the Galileo control system, DECASA can manage all movements, processes and operations taking place within its facility.
The DECASA logistics centre in Mexico - Automated warehouse | |
---|---|
Storage capacity: | +28,000 pallets |
Pallet size: | 1,000 x 1,200 x 1,600 mm |
Max. pallet weight: | 1,300 kg |
Warehouse height: | 34 m |
Gallery
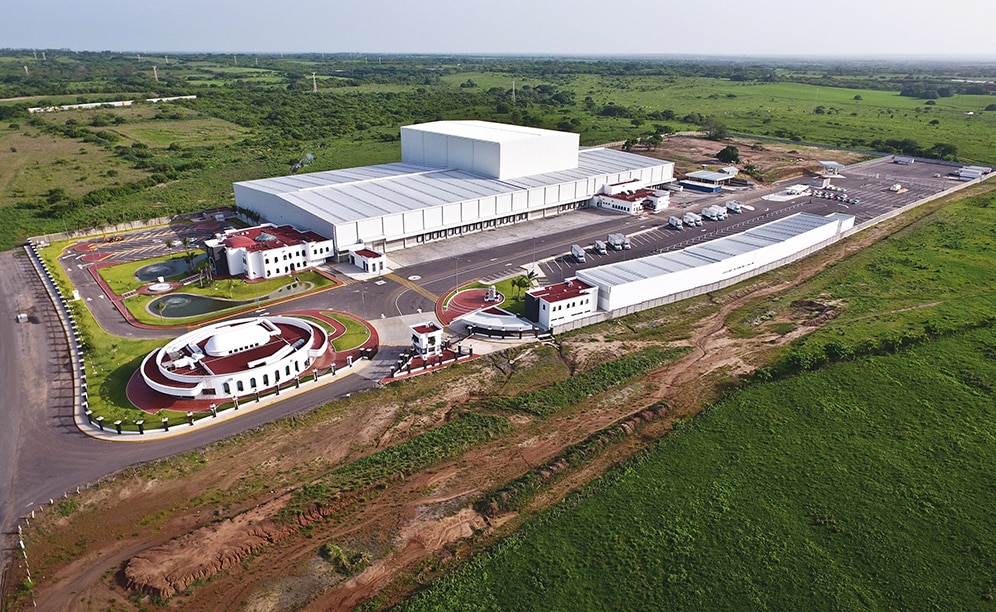
Mecalux erected an automated clad-rack warehouse on a 4,610 m² surface, which is approximately 30 m tall with a capacity for more than 28,000 pallets
Ask an expert